Professor Kamran Mumtaz
School of Mechanical, Aerospace and Civil Engineering
Professor in Advanced Manufacturing
Mechanical Engineering Postgraduate Admissions Tutor
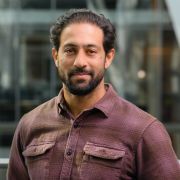
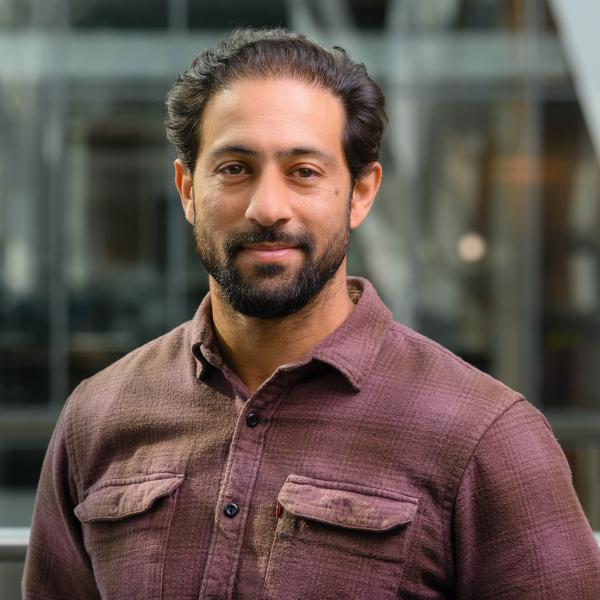
+44 114 222 7789
Full contact details
School of Mechanical, Aerospace and Civil Engineering
Sir Frederick Mappin Building
Mappin Street
ºù«Ӱҵ
S1 3JD
- Profile
-
I obtained my PhD in laser-based additive manufacturing of superalloys for aerospace (2008) and an MSc in Manufacturing Management (2005) from Loughborough University, following a BEng (Hons) in Aeronautical Engineering. Since then, I have been at the forefront of additive manufacturing (AM) research, leading a team focused on developing novel metallic and composite AM technologies. My research aims to enhance material performance, process efficiency, and industrial scalability, enabling the production of high-performance components for aerospace, medical, and energy applications.
Beyond my research, I am committed to developing international research collaborations and fostering global knowledge exchange in additive manufacturing. I actively collaborate with leading research institutions in Mexico, South Korea, and India, working on joint research initiatives, industrial partnerships, and knowledge-sharing networks. Additionally, I play a key role in supporting the postgraduate research network with these countries, strengthening academic partnerships and training the next generation of AM specialists.
- Research interests
-
I specialise in developing advanced Additive Manufacturing (AM) processes for metallic and composite materials, with a primary focus on Laser Powder Bed Fusion (LPBF) and my research aims to enhance material performance, process efficiency, and industrial scalability.
My research has been supported by UK Industry, the Engineering and Physical Sciences Research Council (EPSRC), Innovate UK (IUK), and International funding bodies. These grants have enabled the development of cutting-edge AM technologies and contributed to advancing knowledge in the field of metallic and composite AM.
Novel Manufacturing System Development
To push the boundaries of AM, my team and I develop bespoke AM systems tailored to novel material processing and hybrid manufacturing approaches. This research includes:
- Design and manufacture of multi-laser diode architectures, enabling scalable and efficient melting of metallic feedstock (diode area melting).
- Enhanced thermal control of the melt pool, improving stress reduction, microstructural/mechanical property customisation, and expanding the range of processable alloys.
- Binder jetting technologies for multi-material processing and carbon fibre-based AM part fabrication.
Residual Stress Control & Process Optimisation
A key challenge in AM is residual stress accumulation, which can lead to distortion, cracking, and mechanical failure. My research focuses on stress reduction strategies, including novel laser pre-heating techniques and in-situ monitoring to mitigate thermal stresses, improve dimensional stability, and enhance the structural integrity of AM components.
Multi-Material & Functionally Graded Structures
By integrating different material systems within a single build, multi-material and functionally graded structures offer unprecedented design flexibility. My team explores developing hardware to enable novel alloy composition delivery, microstructural control techniques, and process parameter optimisation to enable seamless material transitions and customised mechanical properties in AM parts.
- Publications
-
Journal articles
Conference proceedings papers
Patents
Website content
- Teaching activities
-
- MEC454 – Additive Manufacturing – Principles and Applications
- MEC333 – Integrated Design Skills
- PhD projects and students
Current PhD Students & Research Projects
- Miss Chunli Wu – Robocasting of ceramic dental implants
- Mr Mehmet Karaman – Multi-material laser powder bed fusion
- Mr Aria Izadi – Thermal gradient control during laser powder bed fusion of tungsten
- Mr Edward Rawson – Use of machine learning for training generative adversarial networks to model diode area melting
- Mr Can Erman – Diode area melting of 316L
- Mr Fathi Alhussadi – Modelling machining conditions of additively manufactured Ti64 components
- Mr Abdul Haque – Thermal management strategies in laser powder bed fusion
- Mr Zaher Alshehri – Multi-laser processing of TiAl
- Mr Zakki Emzam – Multi-material binder jetting of 316L and Cu
- Mr Mustafa Yesilyurt – Laser powder bed fusion of crack-susceptible alloys
Past Projects and Graduated PhD Students- Dr Alkim Aydin (2025) - The use of laser heating for microstructural customisation of Ti6Al4V processed using Diode Point Melting
- Dr Sarath Veetal (2024) - Diode area melting of Ti6Al4V: probing the multi-laser interaction, residual stress evolution, and spattering dynamics
- Dr Halil Caglar (2024) – Hybrid multi-laser powder bed fusion
- Dr Hussam Abunar (2024) - Multi-material metal powder bed binder jetting using PVA binder
- Dr Kubra Genc (2023) - Processing of NdFeB for electric motor applications using selective laser melting
- Dr Busra Karas (2023) - Additive manufacturing of carbon fibre-reinforced polymer composites
- Dr Abdullah Alharbi (2023) – Layered extrusion of metallic alloys
- Dr Sourabh Paul (2022) - Binder jetting of aqueous polyvinyl alcohol for additive manufacturing of Inconel 718
- Dr Mohammed Alsaddah (2022) – Diode area melting of Ti64
- Dr Vimanyu Beedasy (2021) - Investigation into the effects of pulsed laser sintering on inkjet-printed functional materials for printed electronics
- Dr Haider Ali (2020) - Evolution of Residual stress in Ti6Al4V components fabricated using selective laser melting
- Dr Marco Galindo (2019) - Microstructural sensitive model for plastic deformation of Ti-6Al-4V
- Dr Omar Lopez (2019) - Simulation of microstructural evolution of selective laser melted AA-2024
- Dr Miguel Arrendondo (2019) - Diode area melting use of diode Lasers in additive manufacturing of metallic components
- Dr Rafael Martinez (2018) - In situ alloying of elemental Al-Cu12 feedstock using selective laser melting
- Dr Neil Harrison (2015) - Reduction of micro-cracking in nickel superalloys processed by selective laser melting: A fundamental alloy design approach
- Mr Pratik Vora (2013) - AlSi12 In-situ alloy formation and residual stress reduction using anchorless selective laser melting